Brian
The plant was running three full shifts. It had been like this during the fall apple harvest for as long as he could remember. Brian sorted, graded, packed, and now managed the seasonal workforce that processed the new crop of apples, He’d been with the plant since he’d graduated from High School — too many years ago, he thought.
Brian had seen years when the crop had been decimated by late spring frosts. There had been summers when storms delivered rain at the wrong time. The processing plant had been sold three times, each sale resulting in expansion and more automation, fewer employees, and more pressure on the remaining staff. I’m either a survivor or a masochist, he thought, walking toward the break room. By this time, I thought I’d seen everything.
The break room served double duty as a staff room away from the noise of the plant floor. When shift supervisors like Brian needed to pass along information to plant staff, they usually scheduled a meeting before the shift started. Staff were amenable to the arrangement. They clocked in early and were paid for their meeting attendance. For most, it was kind of novel to be paid to drink coffee with workmates in a relatively hospitable environment.
Purdy Apples
Management had called a meeting for all shift supervisors late yesterday afternoon. Good for Brian, the meeting was during his shift and provided a break from the plant floor. Bad for the second and third shift supervisors who needed to make a special trip to attend the meeting. But what do you expect? Thought Brian. Management just work their 9 to 5.
Each time the plant was sold, it was out with the old and in with the new. An international holding company currently owned Purdy Apples. Brian remembered old man Purdy. Mr. Purdy knew apples and was a hands-on boss. Mr. Purdy knew everything there was to know about the plant. Brian remembered him explaining how an old stain on the floor resulted from a forklift transmission blow out. The current management were all graduates from this college or that. They mostly know their stuff, he granted, but they couldn’t care less if they were processing apples or making axles. Spreadsheets, reports, reducing costs and increasing profits — that’s what they’re all about. Brian, on the other hand, was an apple man. He was proud to be a part of the complex process that put apples into the hands and stomachs of so many people.
Management Meeting
Mr. Brad Simmons, the current plant manager, ran the meeting. He began, “You all know that corporate is always on the lookout for new apple markets. They are especially interested in markets that will pay a premium price for our product.”
We supply ten different USDA specified apple products to over twenty nations, what new market has corporate discovered? Brian listened to the younger man skeptically.
“Consumers are told that $160 billion worth of produce are tossed and go to waste every year. They hold companies like ours responsible.” This comment brought some eye rolling. “It’s no secret that big supermarket chains will claim a product is of poor quality and refuse delivery, when the reality is that their sales are slow. It’s also no secret that a good harvest drives down prices with an overabundance of a perishable product that no one wants to buy.”
Kurt, the assistant plant manager from Germany added, “Consumers fear the higher costs associated with a more efficient stable market. They’ve grown used to cheap food.”
Everyone turned back to Brad as he explained that “There is a public perception that much of the waste is due to food being thrown away because it is not up to aesthetic standards.”
Aesthetics! I have a 64-page USDA manual at my desk on the plant floor that tells me exactly how to grade every major breed of apple on the market, thought Brian.
“The word from Corporate is that consumers believe that if people become less particular and are willing to purchase and eat ugly produce, there will be less food waste.”
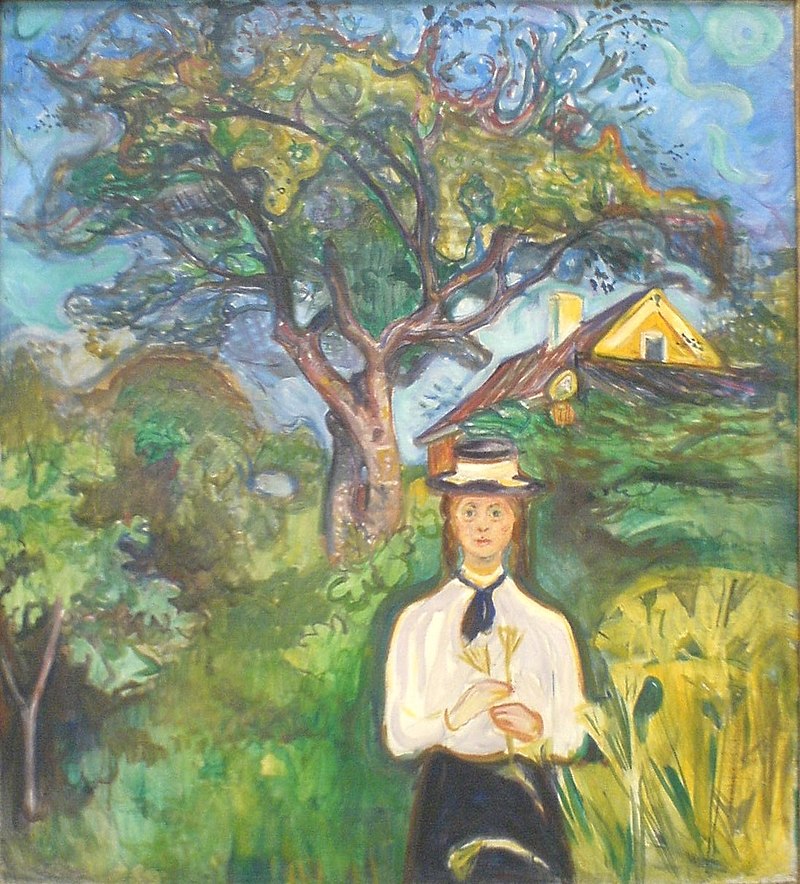
Wasted – Ugly or Not
Speaking for the first time, Bernice Perkins, a comptroller, was incensed. “How is eating ugly fruit going to keep forty cases of large U.S. Extra Fancy Fuji apples from becoming cattle fodder? The were refused by the buyer claiming the fruit was too mature and no longer Firm Ripe.” She glared around the room. “That was a lie. You all know how strict we are in applying tolerances and grading our shipment samples. The driver said he saw cases of unsold Fuji’s in the buyer’s warehouse. The buyer overbought and want us to pay for the mistake. But after being driven around the state for days on crummy roads and exposure to uneven temperatures, the shipment isn’t especially Extra Fancy anymore. The product may no longer even meet minimum USDA tolerances for human consumption.”
A murmur of indignant agreement filled the room. “Nonetheless,” said Brad regaining everyone’s attention, “there is a growing market for so-called ugly fruit and vegetables for socially conscious consumers.”
“Like a Dent and Scratch bin at the supermarket?” said one voice.
“Factory farm seconds?” called out another.
“More or less,” said Brad. “There is another growing niche that corporate wants us to pursue. A number of high tech companies are peddling ugly produce food boxes.”
High-tech? How? Thought Brian. It sounds like the boxes delivered by local subscription farms.
“These companies provide a service that selects, boxes, and delivers imperfect produce to the subscriber’s designated location. Usually, the company provides a phone app so the customer can customize their order. Don’t like ugly zucchini, how about blemished beets?”
No one said anything, but Brad sensed that the management team was not convinced. “People pay a premium for these services. They pay more for misfit produce through these services than they would for premium produce at the supermarket. For people with the means, it’s a way to participate in cutting some of that $160 billion waste and feel good about yourself. Corporate wants our front office to begin building relationships with these new high tech food box providers. We’ll need to work out the supply chain logistics and get a better understanding of how they work. In the meantime, we also need to find out if any of our supermarket customers are planning to jump on the scratch and dent bandwagon.”
Brian Breaks his Code of Silence
Brian had survived multiple plant turnovers due not only to his depth of apple processing knowledge and experience, but also by keeping his mouth shut during management meetings. But he had a burning question. “Mr. Simmons, with all due respect, what exactly is an ugly apple?”
“I’m glad you asked, Brian. We’ve not received any guidance from Corporate. I was hoping that you and the other old hands might help establish an ugly standard for the sorters.”
Brian immediately regretted saying anything as all eyes turned his way. “The bins from the orchards are all sampled and graded according to USDA inspection standards,” he said.
Everyone in the room knew this, but they kept looking at Brian anyway, so he continued. “There are four grades and one subgrade for unprocessed Apples: U.S. Extra Fancy, Fancy, Number Ones, Number Ones with hail damage, and U.S. Utility grade. Samples have to have an aggregate score of 80 or above for nine different tolerances. If an apple isn’t an 80, the FDA says it’s substandard and not fit for people to eat.”
“Maybe the ugly foodies like maggots and worms,” said some wit in the room.
Brian plowed ahead wishing he were back on the shop floor. “Section 51.315 of the inspection guide goes into some detail on what is meant by Fairly well-formed. Maybe the sorters can cull fruit into an ugly bin that score above 80, but where most of the demerit is mostly due to section 51.315 markdowns.”
Brad smiled magnanimously at Brian, “Sounds like a great idea Brian, you and the other shift supervisors get together and make it happen.”
Condescending punk.
Make It So
The meeting dragged on for a little while longer. Afterward, Brian, the other two shift supervisors and M&M — Mike the Mechanic — adjourned to the plant break room. There would need to be a number of minor changes made to the production line they needed to discuss. There was also the small matter of figuring out how to train staff to sort ugly fruit — whatever that was — while interfering with normal operations as little as possible.
Brian walked into the break room and greeted his waiting shift. “Good morning everybody.” A number of people cheerfully returned his greeting.
When it was quiet, Brian said, “Corporate wants a new grade of apple for special customers.”
He reached into the pocket of his white overalls and withdrew an apple. He’d searched the crates earlier this morning to find just the right one. He held it high for everyone to see.
“Hey Chief,” said Manuel, “that is one butt-ugly apple.”
While everyone in the room laughed, Brian observed that the two red lobes did bear more than a passing resemblance to a human backside.
Inspiration
https://www.vox.com/the-goods/2019/2/26/18240399/food-waste-ugly-produce-myths-farms
Credits
Photo of an Apple by Schuyler S(user:unununium272). Taken with 56mm of macro tubes.
https://upload.wikimedia.org/wikipedia/commons/0/0c/Munch_Girl_under_apple_tree.jpg
Edvard Munch [Public domain]